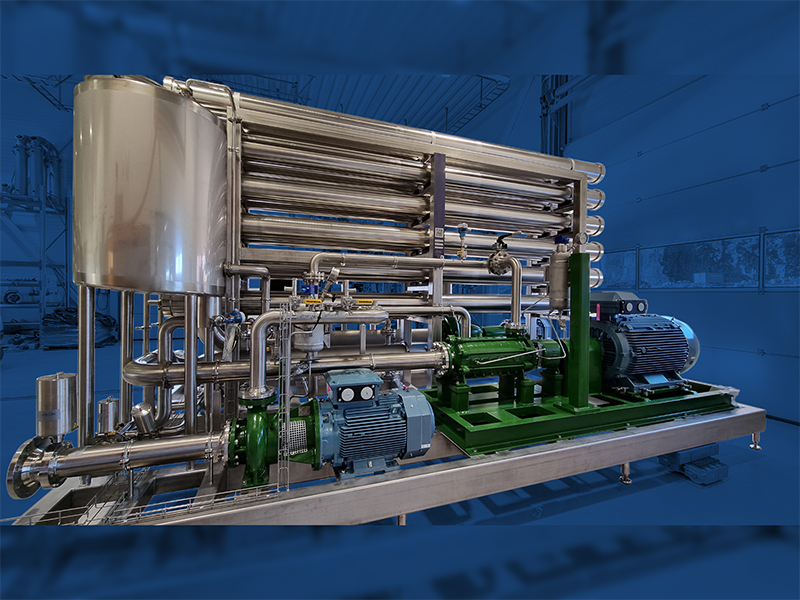
News
The combination of innovative membrane filtration technology and robust Dickow centrifugal pumps revolutionizes industrial filtration processes.
Membrane filter systems are essential in the pharmaceutical, biotechnological, and chemical industries for treating contaminated water and recovering valuable solids. The entire process in such systems is based on the precise interaction of modern membrane technology and specially designed centrifugal pumps that perform various tasks within the system.
The process begins with the supply of the medium to be purified, often raw water with variable contaminants, including concentrated salt solutions. A robust circulation pump, such as Dickows volute casing pump type NCL, sets the water in motion. Its task is to distribute the water evenly over the membrane surfaces and maintain a continuous flow to prevent deposits that could clog the membranes. The NCL pump is designed for continuous operation and conveys large quantities of the medium at low pressure, ensuring an even load on the membranes.
In the next step, a high-pressure pump, such as Dickows multistage pump type HZAR, plays a central role. It generates the necessary pressure to force the medium through the porous membranes. The membranes themselves are made of materials with defined pore sizes that specifically retain contaminants, particles, microorganisms, and even viruses. The pressure generated by the HZAR pump is proportional to the number of its stages; in this system, there are seven stages that generate a pressure of up to 36 bar and enable a continuous flow rate of 70 m³/h. The higher the pressure, the more effective the filtration and the more thorough the purification of the medium.
During operation, residues accumulate on the membranes, which must be regularly removed to maintain the efficiency of the system. The washing and conveying pump, for example, Dickows volute casing pump in block design type NCB, ensures that the membranes are efficiently rinsed and freed from deposits with a high flow rate at relatively low pressure. This not only extends the lifespan of the membranes but also contributes to a consistently high filtration performance.
All pumps used are made of corrosion-resistant materials as they come into contact with aggressive and saline media. Their design is deliberately kept simple to minimize maintenance effort. For particularly low-maintenance systems, the use of magnetic pumps, which do without mechanical seals, is recommended to further reduce maintenance requirements.